Pioneering
Sustainable Dross Processing Solutions Worldwide
TAHA revolutionizes the aluminium industry with salt-free dross processing, maximizing recovery and sustainability. Committed to a zero-waste future, we transform waste into high-value products globally.
81% Percentage of greenhouse gas reduction achieved through our processes

Over 90% recovery of the available aluminium in the dross
Long history of global operational presence and partnerships
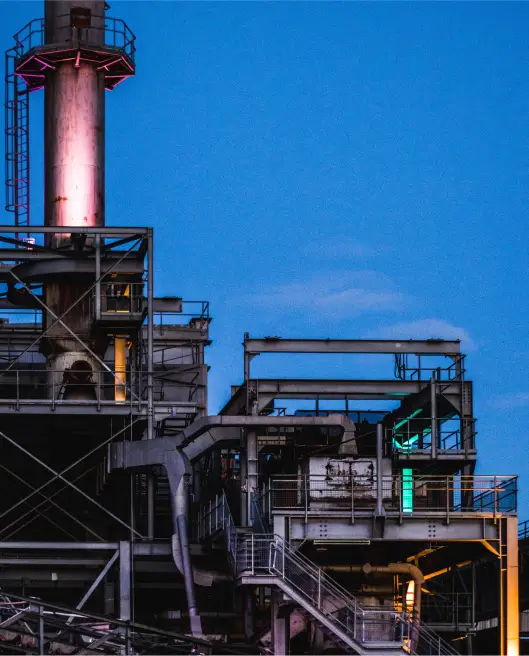
Transforming the Aluminium Industry
Transforming the Aluminium Industry
Leading the Way in Sustainable Solutions and Innovation
At TAHA we are dedicated to fostering innovation, sustainability, and cost-effective solutions. Headquartered in The Kingdom of Bahrain, Taha provides cutting-edge services, equipment, and products to the global aluminium and steel industries.
Through the implementation of our two-stage, salt-free, energy-conserving aluminium recovery process, TAHA's founding principles are accomplished.
Our groundbreaking technology enables us to return a greater amount of metal to primary producers and downstream smelters compared to any other method available.
recovery efficiency
dross globally
TONS
Our Commitment to Sustainability
At TAHA International Corporation, sustainability lies at the heart of everything we do. As a pioneer in aluminium dross recycling and resource recovery, we are dedicated to reducing environmental impact, conserving energy, and minimizing industrial waste.
Zero-Waste Processes
TAHA's patented, salt-free aluminium recovery technology ensures maximum metal recovery while producing no hazardous waste. Residual materials are repurposed into eco-friendly products such as steel slag conditioner, fertilisers, and aluminium trihydrate for flame retardants.
Global Sustainability Partnerships
As a proud member of the Aluminium Stewardship Initiative, we work to establish industry-wide sustainability standards and improve practices across the aluminium value chain.
Innovation for a Greener Future
TAHA constantly invests in R&D to develop cutting-edge technologies and value-added products that benefit the environment and the industries we serve.
Our Commitment
to Sustainability
At TAHA International Corporation, sustainability lies at the heart of everything we do. As a pioneer in aluminium dross recycling and resource recovery, we are dedicated to reducing environmental impact, conserving energy, and minimizing industrial waste.
Notable Partnerships
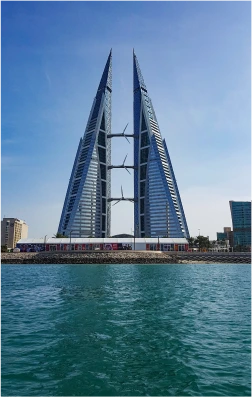
Leading aluminium plants
Bahrain
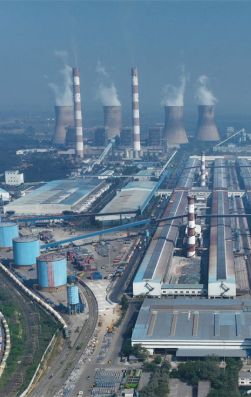
Aluminium plants
India
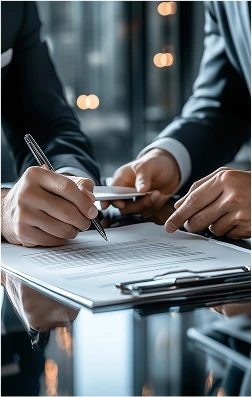
Collaborations with smelters
Global Technology Licensing
Dross Management
The new benchmark in dross processing
Dross should not be considered as waste but as an economic source of valuable aluminium. Dross generally represents between 1% and 10% by weight of the melt, and, depending on the process, its metal content can vary from 15% to 80%. Traditionally, aluminium has been recovered using rotary salt furnaces, which are energy intensive and produce toxic waste.
Patented dross
processing solutions
TAHA’s dross process reduces GHG emissions by 81% vs. TRF
Dross Management
The new benchmark in dross processing

Our Process
Mine
bauxite
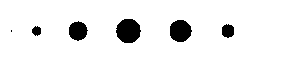
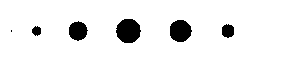
Refine
alumina
Smelt and re-melt aluminium
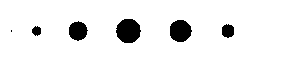
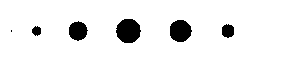
Skim dross in
cast house
FULL ALUMINIUM CYCLE
TAHA OPERATIONS
Our Process
Process hot dross
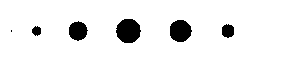
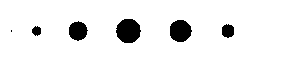
Process cold dross
Final
Products
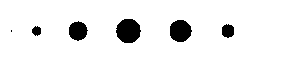
Use depleted dross as feedstock
FULL ALUMINIUM CYCLE
TAHA OPERATIONS
Latest News &
Articles
01
Green Technologies in Heavy Industry
At Runaya, sustainability fuels innovation. Our green aluminium recovery process boasts one of the industry’s lowest carbon footprints, said Jagannath Prasad Routray, CEO, Recycling Business, Runaya, in an interview with Abha Rustagi, Associate Editor, Energetica India.
02
ALuminium Industry: Focus Europe
Europe's aluminium industry excels in sustainability, energy efficiency and innovation, setting benchmarks for decarbonisation and circular economy. This e-Magazine explores Europe’s transformative contributions, market outlook and future prospects, featuring insights from industry leaders.
03
Industry, Logistics & Shipping
The Adnec Group, in collaboration with the Ministry of Defence and Tawazun Council and organised by the Chemical Defence Command of the Ministry of Defence, has launched CBRNE Hub, a new initiative at the International Defence Exhibition (Idex) and Naval Defence and Maritime Security Exhibition (Navdex) 2025.
04
Taha wins IBAAS international award for ESG excellence
Taha International Company for Industrial Services, Bahrain's leading aluminium dross processing company, has been chosen for the prestigious "IBAAS ESG" award by the International Bauxite Alumina & Aluminium Society (IBAAS).
05
Tamkeen supports over 40 Bahraini employees at Taha International
Manama, Sept. 4 (BNA): The Labour Fund "Tamkeen" announced its support of more than 40 Bahraini employees at "Taha International” through the Wage Increment Program and the National Employment Program.
06
Runaya and TAHA extend their global footprint - from India to the world
Runaya & TAHA International, market leaders in aluminium dross processing, have extended their cooperation from India to the rest of the world. Runaya and TAHA aim to set up end-to-end dross processing and refining facilities for major primary global aluminium smelters through a strategic partnership.
Testimonial
Here’s what our customer has to say about
TAHA International
Testimonial
Here’s what our customer has to say about TAHA International
Our partnership with TAHA International has been a game-changer in aluminium dross processing.
Over the past three years, we have deployed TAHA's Hot Dross Processing technology, along with our advanced cold dross processing methods, across multiple Indian smelters. This has resulted in:
- A zero-waste process for producing high-value products from metal-depleted dross residues, further enhancing sustainability.
Jagannath Prasad Routray
CEO Recycling Business Runaya
As a leading manufacturer of secondary aluminium melting furnaces and state-of-the-art casthouse equipment, KMF installed a TRF-like aluminium dross centrifuge at a leading aluminium rolling mill in the Gulf . At this site, TAHA was engaged in a long-term contract for dross processing using its innovative SARAH process technology.
To ensure an objective performance evaluation, dross skimmed from the mill’s melting furnaces was divided into two equal portions: one processed using the TRF centrifuge, the other using TAHA’s proprietary system.
Despite optimizing centrifugal forces to maximize recovery, the TRF system was unable to outperform TAHA’s process.
The result: TAHA’s process delivers outstanding efficiency—without the use of salt or flux additives. This unique, environmentally friendly technology makes aluminium dross processing more sustainable and cost-effective than ever before.
TAHA represents innovation, efficiency, and sustainability—providing a solution that not only maximizes resource recovery but also supports environmental responsibility.
Dr. Oliver Zamal
Chief Executive Officer
KMF Industrial Technologies GmbH
www.kmf.at1
2

Frequently Asked
Questions
Aluminum dross is a by-product of aluminum production, containing valuable aluminum metal and oxides. Processing dross efficiently recovers aluminum, reduces waste, and minimizes environmental impact.
Salt-free dross processing is a method of recovering aluminum from dross without using salt or other chemicals. TAHA’s process is environmentally friendly and energy-efficient, recovering up to 90% of available metal in the first stage.
TAHA’s process involves two stages:
- First Stage: Rapid, low-energy recovery of up to 90% of available metal, which can be returned immediately to the original furnace without further alloying.
- First Stage: Rapid, low-energy recovery of up to 90% of available metal, which can be returned immediately to the original furnace without further alloying.
TAHA’s process eliminates the use of salt, avoiding the production of hazardous salt cake. It also reduces greenhouse gas emissions by 81% compared to traditional rotary salt furnace methods.
TAHA refines the residual oxides into feedstock for value-added products such as steel slag conditioners, agricultural fertilizers, outdoor heat-resistant tiles, and aluminum tri-hydrate (ATH).
By eliminating landfill disposal of depleted dross and converting residuals into valuable products, TAHA’s process supports a zero-waste approach in the aluminum industry.
No, TAHA’s patented solutions do not require additional energy or salt, making the process energy-efficient and environmentally friendly.
Yes, TAHA’s processing facilities are designed to operate in close proximity to cast houses, allowing for easy implementation and flexibility in processing varying quantities of dross.
Yes, the technology can be licensed. You can submit an application to license Taha technology directly through the dedicated licensing section on our website. Here
Frequently asked
questions
Licensing opportunities
with TAHA
Explore the potential of TAHA's proprietary technology in your region. For licensing inquiries, please reach out to us.
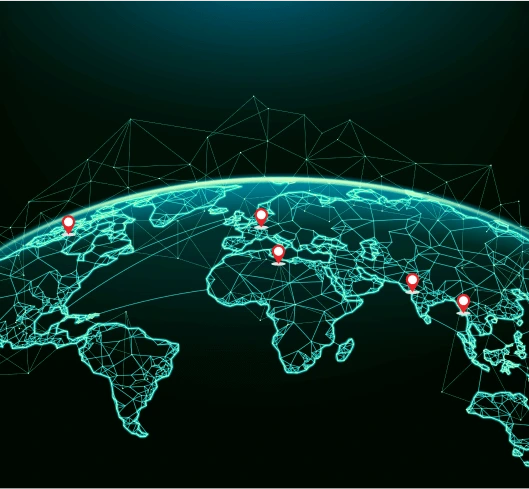